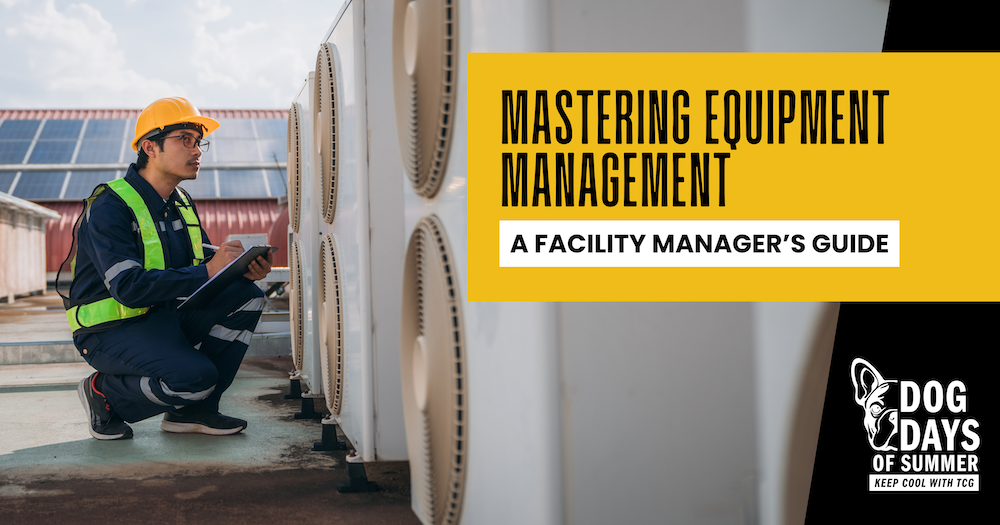
Mastering Equipment Management: A Facility Manager’s Guide
Our Dog Days of Summer series often tackles the most common issues multi-site facility managers face during the sweltering summer months. Today, we’re including an evergreen topic that can impact operations year-round: managing your equipment and understanding your assets.
Knowing the specifics of your equipment—whether it’s the number of air conditioning units, their makes and models, or other HVAC/R, electrical, and plumbing components—is crucial for effective facility management.
In this installment of our Dog Days of Summer, we explore why thoroughly understanding your assets is essential and how it can significantly enhance your facility management strategy.
The Importance of Knowing Your Equipment Assets
For facility managers, having detailed knowledge about your equipment is not just advantageous—it’s essential. Here’s why understanding your assets can significantly impact your operations:
- Optimizing Performance: Knowing each unit’s specifics enables you to maximize its performance. Effective troubleshooting and targeted maintenance become possible, ensuring every system operates at peak efficiency.
- Cost Management: Awareness of each asset’s age, condition, and specifications allows for more accurate budgeting. This foresight helps plan for repairs, replacements, and upgrades, avoiding unexpected costs.
- Preventative Maintenance: A clear equipment inventory allows you to manage preventative maintenance effectively. Regular upkeep can be scheduled and tracked, minimizing the risk of system failures and extending the lifespan of your equipment.
- Compliance and Efficiency: Tracking your assets helps ensure compliance with industry regulations and standards. Regular assessments and updates contribute to more energy-efficient operations, aligning with overall sustainability goals.
Steps to Effectively Manage Your Equipment Assets
To streamline the management of your equipment—whether across multiple sites or a single location—consider implementing these key strategies:
- Organize and Manage a Comprehensive Inventory: Create a detailed inventory of all your HVAC/R systems, plumbing fixtures, electrical components, and other critical assets. Ensure your inventory includes:
- Quantity: Document the number of units or pieces of equipment at each site.
- Specifications: Note the make, model, serial number, capacities, and other technical details of each asset.
- Age and Condition: Record installation dates and assess the current condition of each unit.
- Maintenance History: Maintain records of past maintenance activities and repairs for each piece of equipment.
- Implement an Asset Management System: Adopting an Asset Management System (AMS) can significantly enhance your ability to manage equipment effectively. An AMS helps you:
- Track Maintenance and Repairs: Schedule and log all maintenance activities and repairs to ensure nothing is overlooked.
- Monitor Performance: Analyze performance data to identify trends, potential issues, and areas for improvement.
- Plan for Replacements: Use the data collected to forecast when equipment might need replacement or upgrades, allowing for proactive planning and budgeting.
- Regularly Review and Update Your Records: Make reviewing and updating your asset records a routine practice. Ensure that any new equipment is added to your inventory and decommissioned assets are removed. Regular updates maintain the accuracy and relevance of your asset management system, keeping your records current and reliable.
Collaborate with Your Facility Management Partner
Partnering with a facility management expert, such as Total Comfort Group, can significantly enhance asset management. Our team offers:
- Detailed Site Surveys: A comprehensive site survey is one of the key benefits of working with a trusted facility management partner like TCG. A sampling of our surveys include:
- Collecting information and photos of all HVAC units, refrigeration equipment, exhaust fans, and electrical panels.
- Capturing high-quality photos of the roof layout, each HVAC unit, nameplates, diffusers, return locations, breakers, and disconnect panels.
- Validating existing unit control systems and exhaust fan data plates.
- Capturing high-quality photos as well as the make, model, and serial number of all refrigeration equipment (walk-in freezers/refrigerators, reach-in coolers, ice machines, etc.).
- Discussing HVAC performance and hot spots with store managers.
- Providing a “Google satellite” type overview of RTU layout and specify unit locations (ground vs. roof-mounted).
- Evaluation of all equipment, noting current condition and obvious issues from visual inspection.
[Download a Sample Survey Today!]
- Structured Preventative Maintenance (PM) Programs: Another critical benefit is a well-structured PM program that keeps your equipment in top condition, preventing issues before they arise. Thorough PM maintenance tasks are completed, including:
- Checking belt conditions and tension, clearing condensate traps, and assessing pulleys, coils, and valves.
- Verifying motor operations and documenting any deficiencies or areas needing further diagnostics.
- Ensuring all tasks are performed, and information is recorded accurately, providing quotes for any deficiencies found.
- Expert Assessments: Detailed evaluations of your equipment to identify areas for improvement.
- Customized Solutions: Our tailored recommendations are based on an in-depth analysis of your specific asset data. We use AI-predictive tools to identify trends by compiling data across similar equipment models, such as the most frequently repaired or replaced parts. This allows us to provide actionable insights, helping you effectively plan and budget for maintenance and repairs.
- Leverage Technology for Efficiency: Utilize technology to streamline asset management and improve efficiency. Our modern solutions include:
- Building Management Systems (BMS): Integrated systems that provide real-time monitoring and control of HVAC/R, lighting, and other building systems.
- IoT Sensors: Sensors that deliver data on equipment performance and environmental conditions, enabling proactive maintenance and informed decision-making.
- AI-Powered Predictive Analytics: Our AI tools help predict equipment failures by identifying the top 100 most needed parts and sourcing the best pricing options, ensuring your assets are maintained cost-effectively.
Implementing these strategies and collaborating with a facility management partner like TCG can ensure your equipment is well-managed, efficient, and ready to perform at its best.
Conclusion
Understanding your equipment assets is fundamental to effective facility management. By conducting a thorough inventory, utilizing asset management systems, and collaborating with experienced partners like Total Comfort Group, you can optimize performance, manage costs, and ensure compliance.
No matter what time of year, mastering asset management will keep your facilities comfortable and efficient. For more information on how TCG can support your equipment management strategy, visit www.total-cg.com or contact us today to book a comprehensive site survey of your equipment.
Let us help you ensure that your facilities remain in top shape all year round.